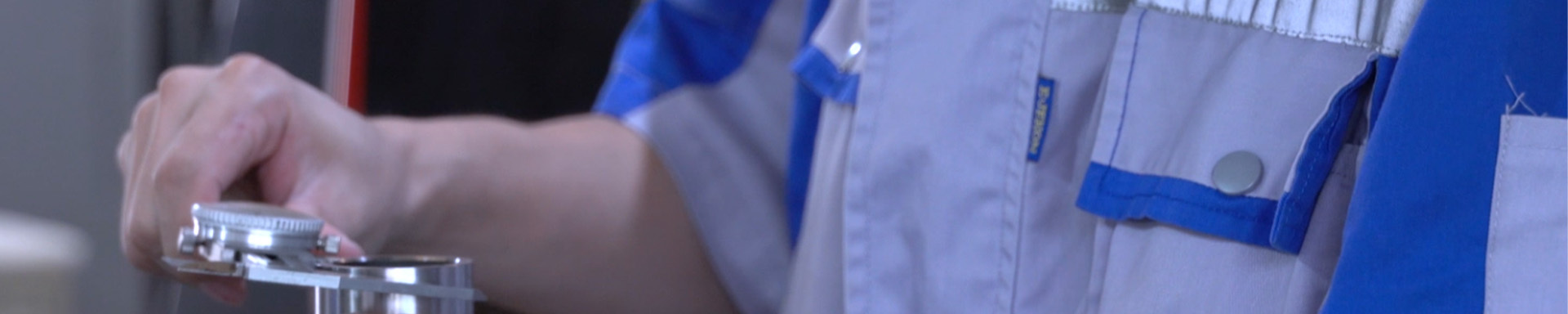
¿Por qué las aleaciones de cobalto son mejores que las de níquel en entornos de vulcanización de alta temperatura?
2025-03-26 09:00En entornos de vulcanización a alta temperatura, la elección del material influye directamente en la vida útil y la estabilidad del equipo. Las aleaciones de cobalto son superiores a muchas aleaciones de níquel tradicionales en condiciones extremas gracias a su excelente resistencia a altas temperaturas, al desgaste, al impacto y a la corrosión. Entonces, ¿qué hace que las aleaciones de cobalto sean ventajosas en entornos de vulcanización a alta temperatura?
1. Estabilidad a altas temperaturas de las aleaciones de cobalto
Las aleaciones de cobalto, como la aleación 6K, mantienen una alta resistencia y dureza por debajo de los 900 °C, lo que les confiere buenas propiedades mecánicas en entornos de alta temperatura. Su excelente resistencia a la oxidación a altas temperaturas se debe principalmente a la película protectora de óxido formada por el cromo, que resiste eficazmente la erosión causada por gases, sulfuros y otros medios corrosivos a alta temperatura.
Por el contrario, aunque las aleaciones de níquel también presentan cierta resistencia a la vulcanización en entornos de alta temperatura, dependen del efecto sinérgico de elementos como el aluminio y el molibdeno, lo que puede provocar una degradación del rendimiento en ciertas condiciones de operación severas. Por lo tanto, las aleaciones de cobalto son más estables en condiciones de vulcanización persistentes a alta temperatura.
2. Excelente resistencia al desgaste y al impacto.
Las aleaciones de cobalto, gracias a su singular estructura de carburo uniformemente distribuida, ofrecen un excelente rendimiento en condiciones de alta tensión, desgaste de partículas o fricción por deslizamiento, reduciendo significativamente el desgaste de los componentes. Especialmente en atmósferas de sulfuro a alta temperatura, donde la resistencia al desgaste de muchos materiales disminuye significativamente, las aleaciones de cobalto mantienen tasas de desgaste bajas.
Además, la tenacidad de la matriz de cobalto proporciona una excelente resistencia al impacto y a los daños por fatiga causados por cargas alternas en componentes mecánicos. Esta característica convierte a la aleación de cobalto en un material ideal para la fabricación de piezas resistentes al desgaste a altas temperaturas, como asientos de válvulas, casquillos de cojinetes, impulsores y anillos de sellado.
3. Excelente resistencia a la corrosión y la oxidación.
El alto contenido de cromo de la aleación de cobalto hace que permanezca estable en soluciones ácidas, agua de mar y entornos de vulcanización a alta temperatura, y tiene una fuerte resistencia a la corrosión del ácido nítrico, el ácido orgánico y otros medios químicos.
En condiciones de vulcanización a alta temperatura, los sulfuros son extremadamente agresivos para los materiales, y muchos metales son susceptibles a la corrosión por sulfuro o incluso a la fractura. Sin embargo, las aleaciones de cobalto, gracias a su composición especial, pueden resistir eficazmente la atmósfera de sulfuro a altas temperaturas y se utilizan ampliamente en reactores químicos, equipos marinos, dispositivos de refinación de petróleo, turbinas de gas y otros campos.
Por el contrario, aunque la resistencia a la corrosión de las aleaciones de níquel es mejor que la de muchos metales comunes, la resistencia a la corrosión de ciertas aleaciones de níquel todavía es limitada en entornos de sulfuro de alta temperatura, lo que dificulta cumplir con los requisitos de funcionamiento estable a largo plazo.
4. Equilibrio optimizado entre composición y proceso.
Las aleaciones de cobalto logran un equilibrio entre resistencia a altas temperaturas, resistencia al desgaste y resistencia a la corrosión mediante el control preciso de la proporción de cobalto, cromo, tungsteno, carbono y otros elementos. Este diseño de material le permite mantener un excelente rendimiento general en condiciones de trabajo extremas, por lo que se utiliza ampliamente en los sectores aeroespacial, energético, petroquímico, fundición de acero y válvulas de alta temperatura y alta presión.
Por el contrario, si bien las aleaciones de níquel se destacan en ciertas aplicaciones específicas, como alta resistencia, bajo coeficiente de expansión térmica y excelentes propiedades electromagnéticas, son menos resistentes a la abrasión y al impacto en entornos vulcanizados de alta temperatura, y su rendimiento general es menos estable que el de las aleaciones de cobalto.
Conclusión: ¿Por qué aleaciones de cobalto?
En conjunto, las aleaciones de cobalto son superiores a las aleaciones de níquel en entornos de vulcanización de alta temperatura con las siguientes ventajas principales:
✅ Mayor estabilidad a altas temperaturas: puede soportar altas temperaturas de hasta 900 °C y las propiedades mecánicas permanecen estables.
✅ Mejor resistencia al desgaste: los carburos se distribuyen uniformemente, lo que les permite sobresalir en entornos de desgaste por fricción.
✅ Mejor resistencia al impacto: la matriz de cobalto le da al material una buena resistencia a la fatiga y al impacto.
✅ Resistencia superior a la corrosión: se mantiene una excelente resistencia a la corrosión en vulcanización a alta temperatura, ambientes ácidos y marinos.
✅ Composición científicamente más optimizada: logra un equilibrio de propiedades entre resistencia al calor, al desgaste y a la corrosión.
Como resultado, la aleación de cobalto es una opción más confiable para condiciones de trabajo severas que requieren alta temperatura, resistencia al desgaste y a la corrosión, y se usa ampliamente en campos críticos como la industria química, la energía, la metalurgia y la industria aeroespacial.
Si está buscando materiales de aleación de cobalto de alto rendimiento, bienvenido a contactarnos, SYTOP ofrece productos de aleación de cobalto de alta calidad para satisfacer sus necesidades especiales.